JIMTOF 2022 hosted a record-setting 5,619 booths at the Tokyo Big Sight convention center. The show featured 1,086 companies from 22 countries. All photos by Modern Machine Shop.
Visiting two of the world’s largest international machine tool trade shows within the span of two months last year was a lesson in contrasts — contrasts between the two host countries, the United States and Japan, and the cultures in which their manufacturing industries operate. But experiencing two technology shows located half a world apart illuminated shared challenges and opportunities more than differences. In fact, the key takeaways from these shows, the International Manufacturing Technology Show (IMTS) this past September in Chicago, and the Japan International Machine Tool Fair (JIMTOF) in Tokyo this past November, were largely the same: The skilled labor shortage in manufacturing is a global problem, and addressing it will involve investments in advanced production systems — high-tech machining centers that link to other shop floor equipment to automate processes, boost production and increase accuracy and quality with minimal human intervention.
JIMTOF 2022 took place over the course of six sun-drenched days in mid-November at Tokyo Big Sight, the sprawling convention and exhibition complex that served as central command for TV and media crews during the Covid-delayed Tokyo Olympics in 2021. The show drew more than 114,000 attendees (fewer than in 2018, in part because of travel restrictions in China due to Covid) and featured a record-setting 1,086 companies from 22 countries and regions around the world. The final booth tally at the show was 5,619 (including 59 exhibitors with 173 booths and the additive manufacturing area), the highest in JIMTOF’s 60-year history.
Featured Content
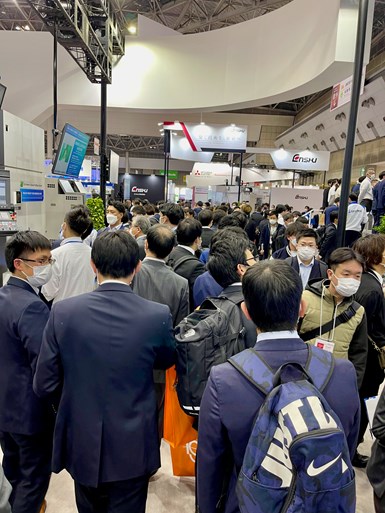
At times during this year’s show, the show floors were so packed with visitors that the aisles were effectively gridlocked.
This was welcome news given the uncertainty that preceded the show, a period of time that included a worldwide pandemic and resulting supply chain issues that wreaked havoc globally across the metalworking industry. During the onset of the pandemic, some machine tool builders were forced to hold off on new product launches while buyers froze capital investments, a situation that created pent-up demand both in Japan and around the world. To a certain degree, that demand has been unleashed. In fact, the latest economic data from Japan showed that machine tool orders in 2021 totaled 1.54 trillion yen — a 71% increase over the prior year. The amount of machine tool orders received during this period was the country’s fourth highest on record.
It will be several months before we know the impact JIMTOF 2022 had on machine tool orders in Japan or elsewhere. In the meantime, here is a glimpse into some of the machinery and technologies I saw at the show. Much like at IMTS this past September, JIMTOF 2022 wasn’t so much a show that featured game-changing technology debuts as it was a show that emphasized new ways to automate through sophisticated integration of new and emerging technologies.
Emerging Tech
Even though the technologies on display in this section of Makino’s booth were meant to showcase automation technologies of the future, most of the tech in this section is fully operational today.
Technology-focused trade shows can sometimes come off like Disneyland’s “House of the Future” from the 1950s — utopian visions of conceptual tech that may or may not serve a necessary purpose or ever come to pass. JIMTOF did not suffer from this condition. Among the larger Japanese OEMs who debuted new machining technology there were Makino and DMG MORI, and both companies’ booths featured interconnected state-of-the art technologies — five-axis machining centers, autonomous mobile robots (AMRs), tool presetters, pallet changers, cobots and workholding stations — staged together and wirelessly connected to work in harmony. In both cases, most of the technology on display is operational today.
In Makino’s booth, one of its iAssist AGVs demonstrated its maneuverability around an obstacle-laden path that surrounded the workstation. There, a mobile cobot mounted on a separate AGV tended to a D200Z five-axis VMC. The system is designed to communicate tool length, workholding settings and other information with the main control for unattended production.
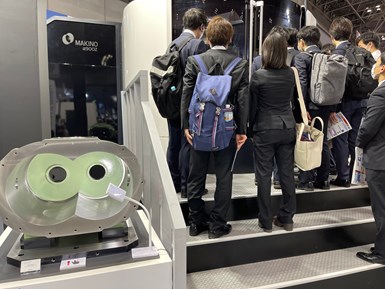
Makino's a900Zm five-axis HMC has target applications that include parts for the semiconductor market, notably the complete machining of chamber housing units used in wafer processing.
In a separate area of the booth, Makino’s DA300, a vertical five-axis machining with an optional 40-pallet pool system, made its worldwide debut at JIMTOF 2022. Next to it and also making its debut — and consistently attracting a crowd — was the much larger a900Zm five-axis HMC (shown here), with target applications that include parts for the semiconductor market, notably the complete machining of chamber housing units used in wafer processing.
DMG MORI’s booth showcased several emerging metalworking technologies, including WH-AMR guide-less self-driving robots and a Haimer Automation Cube.
Meanwhile, one section of DMG MORI’s massive booth showcased a similar choreography of metalworking technologies, with several of its WH-AMR guide-less self-driving robots tending an NXT 1000 five-axis HMC and assisting with loading and unloading parts across a handful of machining centers. In the configuration shown here, the WH-AMR is working with a Haimer Automation Cube — an automated heat-shrink tool presetter that made its debut at EMO in 2021.
Within the Automation Cube is a cobot that exchanges worn cutting tools with new ones, first by grasping the toolholder and presenting the QR code located on its base to a digital scanner, then transmitting that data to the heat-shrink mechanism to inform it how much power and pressure is needed to lock the tool in place. The cobot lifts the newly loaded toolholder to a laser near the top of the cube that confirms that the right tool is loaded before measuring its gage length.
DMG MORI is tackling the “three troublemakers of machining” — chips, coolant and mist — through dedicated features built into its newer machine tools.
DMG MORI also showcased its efforts toward battling the “three troublemakers of machining” — a.k.a chips, coolant and mist. The company’s “Zero Sludge” coolant tanks are fairly straightforward, with nozzles that push any accumulated sludge toward a filter. Its “Zero Fog” feature also uses a specialized filter to collect fine particulate coolant (which can contain oil that will deteriorate machining accuracy as well as operators' health). The company’s “AI Chip Removal” system analyzes chip accumulation using cameras placed inside the machining chamber, then leverages AI to distinguish the chips from the coolant inside the work area and generate a “cleaning path” for motorized chip-flush nozzles.
Okuma’s “Green-Smart Concept” logos represent technologies that are designed to achieve stable dimensional accuracy and reduce energy consumption.
Define “Green”
In our IMTS roundup published this past November, we noted that environmental and sustainability issues are sometimes politically fraught topics in the United States. Not so much in Japan.
For Japanese companies the topic is front-and-center, with chairman Katsutoshi Matsuura of the Japan Machine Tool Builders’ Association openly addressing the global manufacturing industry’s efforts to achieve carbon neutrality during a press conference at IMTS 2022.
When I visited Okuma’s booth at JIMTOF and met with Tim Thiessen, vice president of sales and marketing for Okuma American Corporation, Thiessen acknowledged the cultural contrasts on the issue, but noted that the end goal in both countries is essentially the same, even if the semantics differ. The most prominent logo found at Okuma’s booth (besides the Okuma logo itself) was the “Green-Smart Concept” emblazoned on an array of machining centers. The company defines its Green-Smart Concept technologies as “intelligent machine tools that contribute to resolving environmental issues by autonomously achieving both stable dimensional accuracy and reduced energy usage.”
Okuma’s Genos M560V-5AX, a double-column five-axis VMC that made its worldwide debut at IMTS this past September, consistently attracted onlookers at JIMTOF. The M560-V three-axis VMC is popular in the United States, and Thiessen says that the company has every reason to believe that the new five-axis — which has a similar footprint to the 560-V — will perform similarly well here.
Okuma’s OSP P-500 CNC controller will begin to appear on the company’s machining center products in 2023.
Several of the Okuma machining centers at JIMTOF (like the MU-6300V-L five-axis VMC pictured above) were outfitted with another worldwide debut at the show: The company’s new OSP P-500 CNC controller will begin to appear on its machining center products beginning this year. Okuma says its new controller features faster processing speeds, the ability to perform collision-free machining and similar functionality and ease-of-use between lathe- and machining-center style operations.
Now Introducing
Japanese machine tool builders are encouraged to make technology debuts at JIMTOF. In the member exhibit preview directory, “world debut” technology offerings are called out in each company’s listing with a special avatar. The introduction of forward-looking tech fits with JIMTOF’s reputation as the place to see machine-tool engineering pushing the boundaries.
Besides those listed above, several other major Japanese machine tool builders made world debuts at JIMTOF — far too many to list here. Here are a few other highlights among the many I saw over the course of six days:
This photo was taken at one of several sections of Mazak’s booth on JIMTOF’s first day, soon after the doors opened. The company attracted thousand of visitors over the course of the event.
Mazak’s booth was, simply put, enormous. It was also consistently packed and featured an open-structure, flowing design that contrasted with its equally monumental but modular booth at IMTS. The company made several world debuts at JIMTOF: the FSW-460V friction stir welding machine; the Integrex i-250H AG hybrid multitasking machine with 695/300/1077-mm X/Y/Z travel; and two new VMCs, including the VCN-460+Ez VMC and automation system.
In his inimitable style, Kitamura’s company president and CEO Akihiro Kitamura himself debuted the MedCenter 5AX, a compact five-axis VMC that features a high-speed 30,000-rpm spindle, built-in fifth-axis rotary table and 40-tool automatic tool changer, all of which fit inside a footprint of just 28 square-feet.
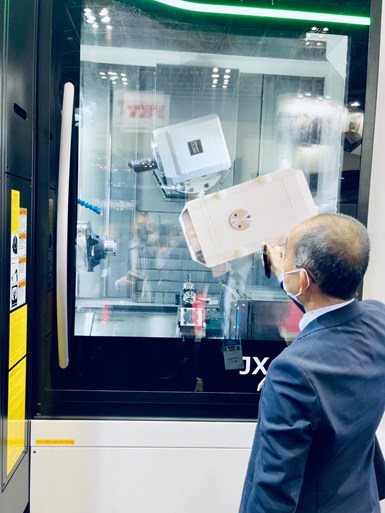
A cardboard cutout shows the size of the former tool spindle model versus the new model included in Nakamura-Tome’s JX-200 multitasking machine.
Nakamura-Tome made its Asia debut of the JX-200 ATC multitasking machine for gear skiving and other complex operations. The machine features an updated, more compact version of its “Smart Cube,” which the company markets as the “world’s shortest tool spindle.” Shown here, the company even brought a cardboard cutout of the previous version for comparison.
Marubeni Citizen-Cincom debuted its compact RL03 chucker-type CNC lathe that features single-slide construction and roller guides that minimize thermal displacement. Suited for production lines, the entire machine has a width of just 700 mm.
Tsugami introduced both its P036W CNC precision automatic lathe that features a 20,000-rpm spindle and 18-tool toolholder and its B0206-V CNC precision automatic lathe that holds 27 tools. Matsuura debuted two new five-axis machines, including the MX-330 PC10 five-axis VMC with an 80-kg loading capacity and the MAM72-42V PC21 five-axis VMC.
RELATED CONTENT
-
Tackling the Aerospace Supplier’s Dilemma: Scalability
Automation and robotics can go a long way toward increasing capacity and growing a business dedicated to aerospace manufacturing. But Trinity Precision has learned that refining the indirect and unseen aspects of its operations can be just as valuable.
-
Watchmaking: A Machinist’s View
Old-world craftsmanship combines with precision machining on a vertical machining center and Swiss-type lathe to produce some of the only U.S.-made mechanical wristwatch movements.
-
Palmgren Launches Combination Bench Lathe, Mill
The 11" bench engine lathe and gear head mill is able to handle a wide range of turning, milling and drilling operations typically found on much larger machinery.