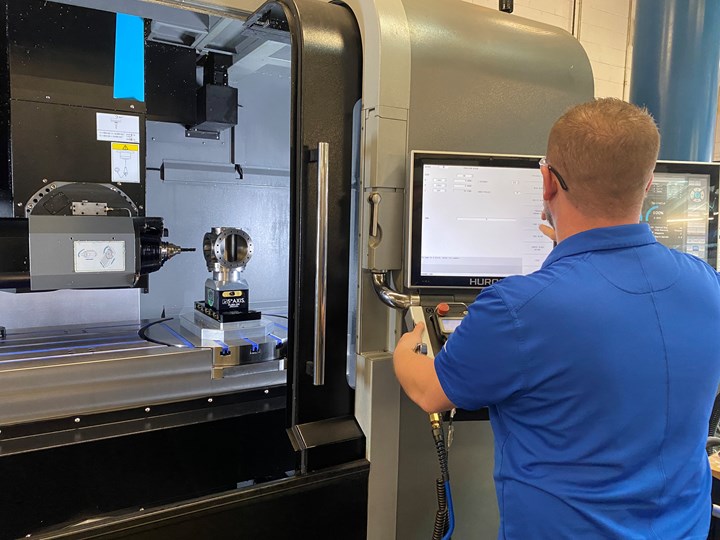
Machine shop supervisor Kenny Urban stands at Meyer Tool and Manufacturing’s first five-axis machine, a Hurco VMX42SRTi. The shop added this machine five years ago when it won a bid for a particularly complex part.
“We take on a lot of that work that other companies shy away from because it's complex,” says Kenny Urban, machine shop supervisor at Meyer Tool and Manufacturing. “Our motto is we build the impossible.”
Meyer Tool’s reputation for building the impossible started when Frank Meyer founded the company in 1969. Meyer, a machinist at Argonne National Laboratory, saw layoffs coming and set up his own shop in his garage with a lathe and a Bridgeport. Soon, he was bidding on jobs fabricating pressure and vacuum vessels for Argonne, as well as other national laboratories.
Featured Content
To make these parts, the company, which is now run by Frank’s daughter, Eileen, is vertically integrated with engineering, machining, welding, assembly and testing services at its Oak Lawn, Illinois, facility. The machine shop is comprised of 14 machine tools (a combination of manual and CNC milling and turning machines) and six employees.
Prototyping and R&D work from labs and private companies has provided Meyer Tool a strong foundation. Although making parts for complex projects like particle accelerators is fulfilling work, it’s looking to expand its customer base. Urban says the company’s goal is to reach 70% OEM work, with more higher-volume and repeat jobs.
In order to accomplish this goal, it’s open to adopting new technologies. “Let's say we do get a huge contract with a high volume. We have no problem going out and getting that cobot or investing in ourselves to be able to take on that kind of work,” Urban says. “We're open to pretty much anything that can come our way.”
This is how the company acquired its first five-axis machine five years ago. One of Meyer Tool’s customers approached the shop with a part. The shop is one of a few approved vendors for this customer, so it knew it had a good chance of winning the job. But the part was very complex — a dome with multiple threaded holes and a water channel that curved all the way around the top of the part. Urban knew it would require five-axis machining. The shop had been considering a five-axis machine for some time, and with this job, it decided the time was right to purchase a Hurco VMX42SRTi.
“Today’s quotes are won by price and lead time. Having a five-axis machine gives you the advantage of both.”
The VMX42SRTi features a B-axis swivel head and a C-axis rotary table that’s flush with the machine table. This configuration, combined with its 50-by-24-inch table, gives Meyer Tool flexibility. The shop can machine large parts, such as the dome, which was more than 2 feet in diameter. Or, instead of one large part, the extra space can be used for more than one part.
“I have a whole table that I can throw another vise on and now I can do multiple setups in one machine, which is really nice,” Urban says. The B-axis head can access most areas of these parts for machining.
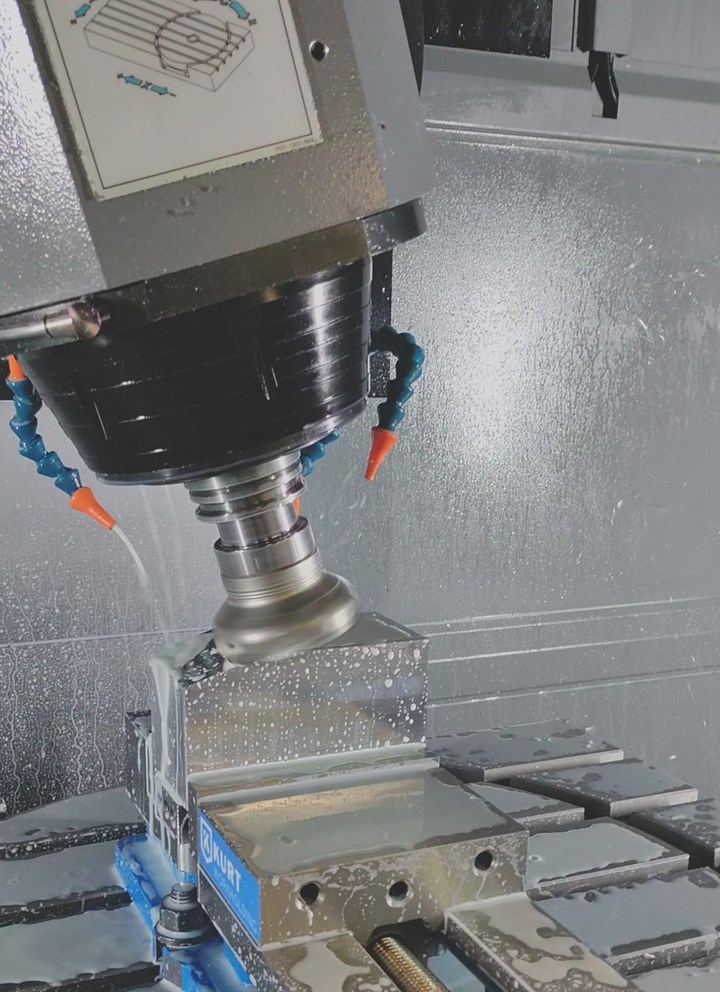
Instead of a trunnion table, the VMX42SRTi is configured with a B-axis swivel head and a C-axis rotary table that’s flush with the machine table, enabling Meyer Tool to machine larger parts, or set up multiple parts in the machine at once. Photo Credit: Meyer Tool & Manufacturing
Polar Exploration
The machine itself was just one piece of the puzzle needed to complete the job. Next, the shop had to figure out how to program for five-axis machining. The part required full five-axis contouring and surfacing, which Urban had never programmed before. The part’s size, which was larger than the machine’s rotary table, added to the challenge.
As Urban was researching five-axis programming, he came across a YouTube video from Hurco Europe that showed polar milling on the VMX42SRTi. Polar milling is a strategy that locks the machine’s Y axis, and all of the Y-axis movements are transferred to the C axis. “Essentially, you can program bigger parts than your envelope, and keep all your movements right in the middle of the machine,” he explains.
The program being used in the video was Autodesk Powermill, and Meyer Tool invested in it based on the polar milling capability. Urban knew the shop would be able to use this strategy on other jobs because many of the parts it machines are larger than the VMX42SRTi’s work envelope.
This strategy also has the benefit of producing tighter-tolerance parts. “Anytime you can limit excess movement, you're going to have a more precise part,” he notes. When the X, Y and Z axes are all moving, that’s three axes and three ballscrews that have to move. But if only the C and X axes are moving, that eliminates additional motion that could negatively affect part quality. For example, Urban used polar milling on a recent part to reduce chatter when roughing with a three-inch endmill. “When I was coming to the front of the part where there wasn't as much support, the cutting tool was starting to vibrate and chatter,” he says. “So I decided to jump on Powermill and change it to a polar milling tool path. And it just stayed right in the middle of my table and reduced the chatter.”
Urban says five-axis programming was scary at first because the code is more complicated than three- or four-axis machining. But Autodesk and Hurco worked with him closely on that first part, even signing NDAs with the customer. “I had Autodesk walking me through how to program it, and I had Hurco there showing me how to set it up,” he says. “It was a really cool partnership.” Urban has since taken training through Autodesk, and plans to take more in the future.
The shop also works closely with NexGenSolutions, which provides support and training for Autodesk software. “Whenever I'm stuck on something, it's literally a ticket away,” he explains. “They jump on my computer, and they walk me through and train me and show me how to do it as I go.”
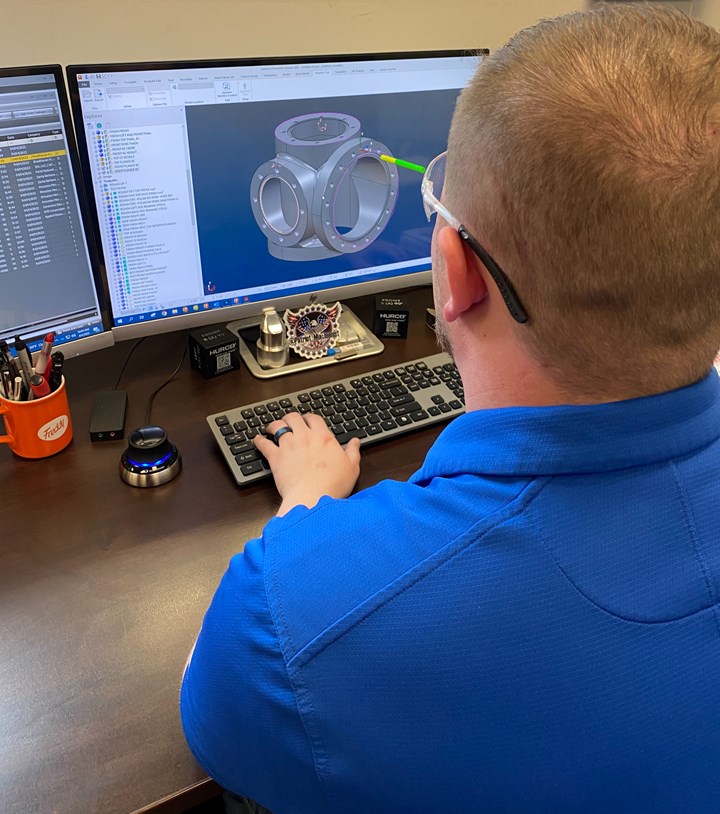
According to Urban, most of Meyer Tool’s five-axis parts don’t require full simultaneous five-axis toolpaths. The majority are machined positionally, which can be programmed conversationally at the control or at a desktop computer.
A Conversation Piece
Not all of Meyer Tool’s five-axis work requires full, simultaneous five-axis motion. In fact, Urban says most of the shop’s five-axis jobs use five-axis positional machining. These jobs can be programmed conversationally via the control. Hurco’s control uses WinMax software, which supports a feature called Transform Plane that’s designed to make conversationally programming five-axis position work intuitive. Urban says Hurco provided a training block with the different planes labeled, which he uses to determine how to transform planes during conversational programming.
The control also supports concurrent programming, which enables users to program at the control while a different program is running. Users can also maximize spindle uptime by creating conversational programs on a computer using WinMax Desktop software and then sending them to the machine.
Urban says surface finish is one of the biggest factors when planning whether to use positional or simultaneous five-axis machining for a given part. “Let's say I have a part that has to be pristine. I’ve got to have it look like a mirror,” he explains. “I'm going to use simultaneous because I know that I can keep the tool on the part the entire time with no lifting up and going back and forth.” With three-axis or five-axis positional machining, the tool is coming in and out of contact with the part as it’s repositioned, and the dwell marks this creates negatively impact surface finish. Urban also jokes that he considers full five-axis motion “if I want to make a cool video.” (He frequently posts machining videos on his Instagram account, @patriot_mucheenist.)
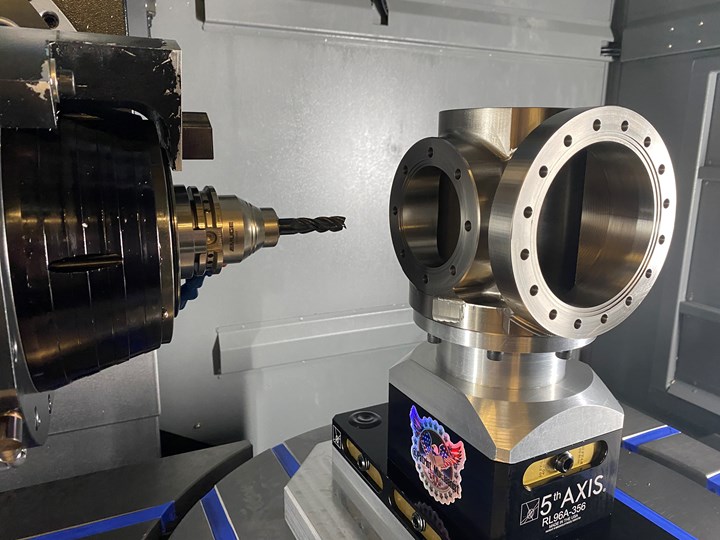
Five-axis machining saves Meyer Tool a significant amount of time by reducing setups, as illustrated by this part. According to Urban, “With all the different setups, flipping and everything, I would probably say (the five-axis machine) saved me at least 30 hours’ worth of work.”
Setting Up for Lights Out
As with the first job, five-axis machining has enabled Meyer Tool to take on work it previously couldn’t do — parts that are more complex or have tight tolerances. But the shop is also able to make parts it previously would have run on a three- or four-axis machine more efficiently, which helps it win more work. “The market is very competitive, especially with lab jobs,” Urban notes. “Sometimes they get bid out to hundreds of different companies.”
Five-axis machining is particularly beneficial to high-mix, low-volume shops like Meyer Tool. “We're a custom fabrication shop and we do something new every time. Setup could be at least an hour, gathering what you need and putting it all together. So we're able to cut down the time quite a bit.”
The reduced number of setups on the five-axis machine has enabled Meyer Tool to do more lights-out machining as well. Running lights-out also requires a certain level of confidence in the process and machine. “We did not do lights-out machining very often before getting the VMX42SRTi,” Urban notes. “I think it's because we trust this machine so much.”
The shop maintains this trust through regular machine maintenance — it has the machine serviced and calibrated every year. Urban also has confidence in his programs because he can use the control or WinMax Desktop software to check for errors before running them. And Urban can use Hurco’s Extended Shop Floor program to remotely monitor the machine from a computer or phone when running unattended. It shows information such as machine status and load meter, and includes a live feed from a camera inside the machine. With these controls in place, Urban says he runs lights out as often as he can.
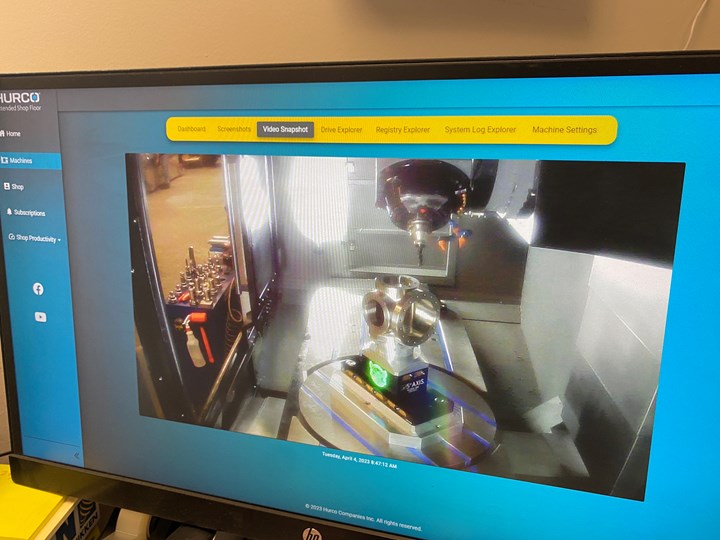
Regular machine maintenance, the ability to check programs for errors via the control or WinMax Desktop software and machine monitoring capability through Hurco Extended Shop Floor provide additional reassurance when running unattended.
The Best of Both Worlds
The VMX42SRTi has been a big success for Meyer Tool, so when Hurco gave the shop the opportunity to beta test a new five-axis machine as part of its Hurco Pro shop partnership, it jumped at the opportunity. At the time of my visit, the shop was awaiting a VMX30UDi trunnion-style five-axis machine, which will give the shop added five-axis capacity as well as variety in its five-axis capabilities. The VMX42SRTi’s swivel head can’t reach the very bottom of a part unless it’s on risers that are high enough for the swivel head to get underneath the part. The risers are possible with the shop’s RockLock modular workholding system from 5th Axis, but this setup is not always ideal because it can be less stable. “Now we'll have the best of both worlds,” Urban says.
The VMX30UDi also has a larger capacity toolchanger, with room for 60 tools instead of Hurco’s standard 30. Urban says the extra tooling capacity will help with smaller parts (which he notes tend to use more tools than larger parts). It will also be useful for redundant tooling, which, when combined with a tool probe, will aid in lights-out machining.
Ultimately, five-axis machining has enabled Meyer Tool to make parts cheaper and faster. Urban believes this capability is becoming a necessity for shops to compete. “Today’s quotes are won by price and lead time,” he says. “Having a five-axis machine gives you the advantage of both.”
RELATED CONTENT
-
Can ChatGPT Create Usable G-Code Programs?
Since its debut in late 2022, ChatGPT has been used in many situations, from writing stories to writing code, including G-code. But is it useful to shops? We asked a CAM expert for his thoughts.
-
Investing in Automation, Five-Axis to Increase Production Capacity
To meet an increase in demand, this shop invested heavily in automation solutions and five-axis machines to ramp up its production capabilities.
-
Hermle Event Encourages, Educates on Five-Axis Machining
Hermle’s first Five-Axis Summit was designed to show beginners the benefits of five-axis machining and demonstrated how more advanced users can take their capabilities to the next level with automation.